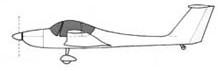
Maintenance Manual GROB G 109(Adapted from photocopy supplied by GFA c1990)
Subject of inspection &/or maintenance
Section 1. Engine (clean)
1. Cowling: check for cracks, dents and loose or missing connectors
2. Fire resistant colour check, correct damaged areas (Wiedoko 4 -Brandschutzfarbe N 56582/weiB)
3. Valve rocker clearance adjust , cold (inlet/exhaust: 0.2 mm / 0.008 in. ) (slightly more with cast iron barrels – 0.010in)
4. If necessary, replace rocker box cover gaskets
5. Remove spark plugs from cold engine, check gap 0.4 mm (0, 016 in. ) and clean with plastic brush.
Recommended spark plug exchange interval: 150-200 hours (Note 2)
6. Compression check ( for further details consult engine manual)
7. Check for leaks at oilpressure and temperature sensors
8. Perform oil change (warm engine /max. 2.5 litres )
9. Clean sump oil screen
10. Fuel lines – check for leaks , safety-wired and wear.
11. Remove fuelfilter cap, clean screen, install and safety-wire.
12. Oil level check of Stromberg- Zenith carburetors
13. Carburator diaphragm check and fill up Zenith lube oil (for further details consult engine manual )
14. Airfilter check, clean and damp with oil
15. Electrical wiring check for damage, wear and secure attachments.
16. General condition of clamps, fittings and linkages (Throttle, choke , and carburetor linkages)
17. Engine mounts check for cracks, looseness of mounts, and looseness of engine to mount.
page 23a
18. Check alternator drive belt tension and condition
19 Time magneto to engine (for further instruction consult engine manual)
20. Fuel pump: clean screens (both electric and mechanical)
21 Check ignition harness for security of mounting clamps, damage and tight connections at spark plug and magneto terminal
22. Mounting of starter,alternator and magneto secure and tight.
23. Starter wheel check for damage.
24. Check crankcase for leaks and cracks.
25. Cooling ribs of cylinders clean, no cracks or other damage.
26. Crankcase breather line secure and tight.
27. Lubricate magneto snapper with appx. 10 drops. of oil.
28. General condition of exhaust system, corrosion and burnt-through areas and remove heat exchanger. Check attaching flanges at exhaust ports of cylinder for evidence of leakage. If leaks exist, remove exhaust system, machine flat and re- assemble with new gaskets (Subaru or Beetle 1300) (Note 1)
29. Heat exchanger condition and tightness
30. Fresh and warm air hoses check for leaks and general condition
31. Fresh air duct panels tight and no damage
32. Fire wall grommets and fairleads (sic) condition
Also at 50hrs: Carb diaphragms, time magneto.
Page 23b:
Propeller (see also Owners Manual for variable propeller models HO-V62/HO-62R)
1. Remove spinner and check for dents, cracks and roundness.
2. Check blade installation or absence of blade shake and radial play (angle) to one degree.
3. Check blades for absence of cracks and damage.
4. Watch smooth operation of pitch change.
5. Pitch adjustment, ball bearings, thrust plate without cracks , wear, play and dirt. The wear of the plate must be less than 0.2 mm (0.008 in.)
6. Grease the four studs with Calypsol H 442 or equivalent.
7. Check visible hub parts for cracks and corrosion.
8. Slightly grease tracks of ball bearings with Calypsol H442 or equivalent.
9. Pitch limiters without large friction.
10. Check torque moment of stop nuts at the flange attachment of the prop by applying torque 4,5 mkp (390 in/lbs. ) without loosening the parts. (32.5 ft/lbs – rjw)
11. Inspect prop blades for even. (sic) (Note 3)
Page 23c
Section 3. Airframe
1. Surface-check for damage, inspect cracks, painting & markings.
2. Pitot tube, jacking rings, airbrake panels & position light covers secure.
3. Lubricate springs of airbrake panels
4. Aileron hinges: check for corrosion & operation & slightly lubricate
5. Drain holes clear.
6. Wing fittings check for corrosion & slightly grease.
7. Quicklock fasteners of airbrake & aileron control assy. Inspect for proper operation.
Grob AD Hotellier in Tailplane: measure w/micrometer 100 hourly & grease 50 hourly.
(Note 1) Removal of rust followed by a liberal application of aluminium grease helps keep the steel flanges in good condition and makes it easier to keep an eye on the weld between the steel flange and the stainless steel header pipe. Exhaust pipe gaskets (the round ones between the header and the muffler) are small diameter type from early Beetle 1300, not the later 1500 type.
(Note 2) An unauthorised but very simple solution to a common sparkplug problem is to fit two copper plugwashers instead of the usual one. This brings the tip of the plug thread fairly level with the face of the combustion chamber, preventing deposits building up on the protruding threads and also alleviating problems with the cylinder head temperature sensor. This trick is also used in the Byron Gliding Club’s MotorFalkes. It works with Champion REL37B plugs, and may work with Bosch WB240ERT1 plugs.
(Note 3) To check evenness of prop blades, place a marker close to the tip of one blade, then rotate prop 180 degrees. Marker should be within 5mm or so – the propeller manual should state the limits. Periodic checking of tacho accuracy is also recommended.
Cooling: In Australian conditions, the standard G109 Limbach motor tends to run very hot. Fitting a Kombi oilcooler, a NACA duct to the cooler, and an extended sump (and running Penrite oil) has solved the problem – the oil temp remains below the red even in the hottest outback summer conditions, and generally settles down to about 80 degrees during cruise. It actually runs a bit cold in winter.
If Penrite or similar quality oil is unavailable, expect a ten degree rise in temperature and lower oil pressure.
Rudder Removal can be quite tricky. Here’s how to make it simple.
Tailwheel Assembly information
Miscellaneous
Alternator Belt – 10*500 Continental RO-HT-FZ
(numbers printed on Continental belt: FO10/Z 520 LiZ 20 1/2
Alternator: Ducelier 22/30A (some have Bosch alternator)
Alternator Brushes for Ducelier: Bosch brushes may be modified for the purpose.
Brakes – see menu or search box.
Carburettors – Stromberg 150 CD-3 – see page
Electric Fuel Pump – Hardi model H cat 2212. – see page
Magneto – Slick 4230 – see page
Bearings: Tailwheel 6004LLU, Mainwheel 6006RS
Bearings: Propeller pitch actuator fork – see propeller page
Carpet – Cockpit: Happich 7720033
Crankshaft and conrods: Porsche 914
Starter Motor – Fiat, Bendix type. – see page.
FFN: Current engine is a Porsche 914 based Limbach with a heavy duty crankcase and running dual plug heads. Rated at 80hp @ 3300, but rarely sees more than 3000 in the climb due tipspeed limitations. It cruises 2650/2700 at 80/85 knots but is quite happy to go faster. True max horsepower I would guess around 60/65. Dual CV carbs by Stromberg provide excellent economy – 13 litres per hour.Fuelburn 1 hp for 1 hr 0.284 litres of fuel per hr.
Therefore 13 litres / hr divided .284= 45.77 HP
Propeller Pitch Adjustment – see propeller page
Grob 109 Torque figures
Propeller flange nuts torque: 35-37 ft/lb, 48-50nm
Cylinder Head Torque 12/18 ft/lb (check this!)